Do you want to optimize your tissue process? Go pilot with Valmet!
Sep 16, 2024
To help tissue makers secure their future success, Valmet offers an opportunity to optimize and develop the complete tissue making process and end products in our pilot facilities in Sweden, Italy, USA and Brazil. Valmet’s experienced R&D teams can guide you through the whole development process from raw material to finished end products, i.e. from stock-preparation to tissue making and converting. The pilot centers can of course also be used separately for developing and optimizing according to individual customer needs.
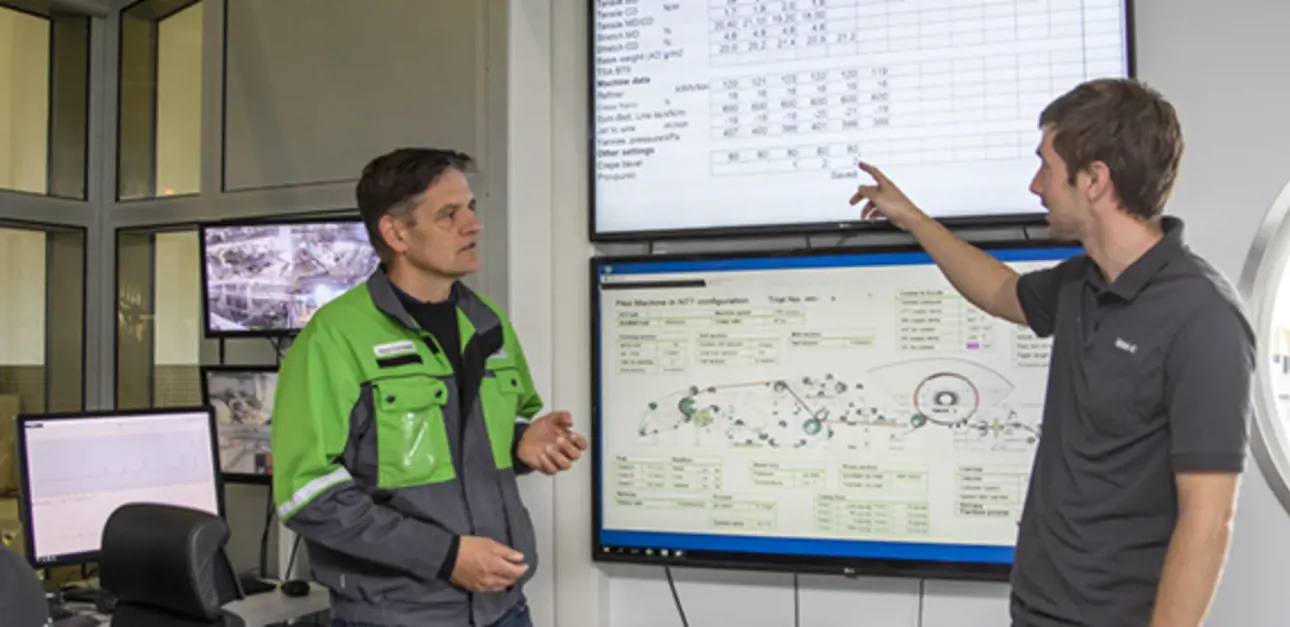
A pilot trial at Valmet offers tissue producers a cost-efficient, flexible way to test and evaluate new ideas without disrupting daily production, unlike testing on a commercial machine. Likewise, determining the operating window for a specific process or product is easier in a pilot facility environment.
The pilot trials at Valmet Tissue Technology Center in Sweden are focusing on the paper making process, with the target to help customer developing machine performance, efficiency, product quality or testing new raw materials or configurations.
The labs and pilot lines in Italy, the USA and Brazil are testing and developing converted paper quality. They provide evaluation of paper strength, absorption, thickness and softness for durability and comfort. The geometric and physical characteristics of the finished product are also analyzed to meet quality standards. Additionally, the converting pilot lines conduct comparative analyses of market products and offers consulting services to optimize production processes and improve product quality.
Concern for climate and sustainability steer development efforts
The biggest global concerns of our time, such as climate change and scarcity of natural resources, have driven the need for more stringent climate and sustainability related requirements also for tissue production.
Tissue producers are focusing on increasing resource efficiency and adopting new raw materials to meet tightening climate and sustainability requirements while staying competitive. Further development of attractive and competitive consumer products is also on their to-do list. The priority these hold on different producers' agendas depends on the markets they serve and the end-use areas their products represent.
“We clearly see that new raw materials are coming strongly to tissue making in the Asian markets. At our facility, customers have conducted pilot trials with straw, bamboo and bagasse, to name a few. The development of production processes suitable for these raw materials is an interesting focus area. On the other hand, in the very competitive North American markets it is important to be able to introduce new attractive consumer products regularly,” says Hans Ivarsson, Project Manager, R&D, at Valmet’s Tissue Technology Center in Karlstad, Sweden.
Making pilot trials easy for customers
Valmet has put a lot of effort into making the pilot trials as easy as possible for customers – from planning to the actual trial run with laboratory services readily available.
“No matter if a customer wants to optimize consumer products, improve machine properties or the blend of water, fiber and chemicals, or cut consumption figures – we can do it all,” Ivarsson says.
Planning starts months before the trial, and is based on the customer’s needs and targets, to ensure the best possible test run.
A wide range of machine configurations available
Valmet Tissue Technology Center in Sweden provides the broadest selection of machine configurations in the world. The machine provides many different concepts and configurations covering conventional, plain tissue, the advanced TAD process for premium-quality products, and hybrid processes for plain and structured tissue paper. Hybrid processes enable high quality textured and structured tissue with less energy consumption compared to the TAD process. In addition, different customer-specific, confidential configurations are also possible.
Having a laboratory next to the pilot machine is a big advantage and means that samples can be analyzed very quickly. It takes only 10 to 15 minutes from the sample entering the laboratory before trial parameters can be changed based on the test result and the test run can continue. It is possible to make up to 20 changes per day to reach the customer’s targets, if needed.
Reliable test data supports customers’ decision making
Pulp and paper samples are analyzed for basis weight, absorbency, layer purity and tensile stretch, for example. The possibility to compare the results with Valmet’s extensive test data bank ensures stable and reliable test results. After the test run is over, the tissue rolls produced are delivered to the customer or to the Tissue Converting pilot lines for converting and market testing. “At our pilot facility, we can engage with and support the customer at every step of the tissue production process. In addition to our own extensive expertise, we can bring in specialists from different disciplines as well as partnering vendors.”
|
|
After the trial, customers are provided with a comprehensive, high-quality test report that has real and reliable production data they can use as a basis for their investment and other decisions.
In times when traveling is restricted, or a customer is prevented to visit in person it is still possible to follow the trial. By web camera and digital connection, a customer can be part of the test and get production data instantly.
Valmet Pilot Centers operates under strict confidentiality and all information is handled with great respect to customers confidentiality needs.
“One thing is clear. There is a visible correlation between business success and market position and the R&D work being done by the tissue produces who chose to utilize Valmet Pilot trials on regular basis,” concludes Ivarsson.
Pilot trials at Tissue Converting
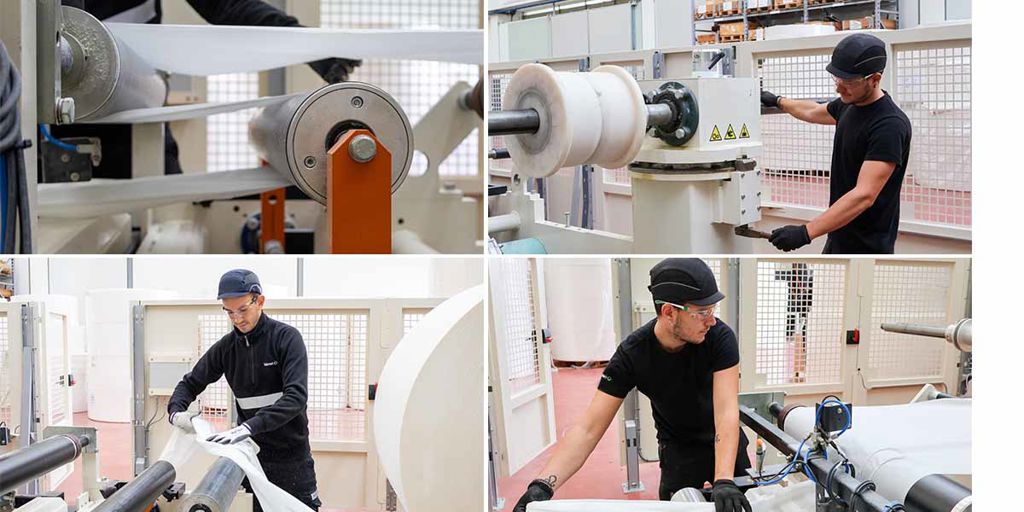
The Tissue Converting piloting offering is truly comprehensive and integrates Valmet’s three areas of excellence into a single value chain: Fabio Perini and MTC for converting and packaging technology, Pivot LAB dedicated to high-level measurement and analysis to predict, understand and anticipate market trends. Finally, Engraving Solutions in Italy and Roll-Tec in Brazil, with two low-speed pilot lines for folding and converting, create products aesthetically similar to real production performance. In Lucca, a modern facility features a climate-controlled laboratory, maintaining humidity and temperature to conduct analyses in accordance with ENI UN ISO 12 6625 standards.
Valmet Tissue Converting operates labs and pilot lines in Italy, the USA, and Brazil to test paper quality, assessing strength, absorption, thickness, and softness. They also analyze the physical characteristics of finished products to meet quality standards. Pivot Solutions provides comparative market analyses and consulting services to optimize production and improve quality.
Valmet Tissue Technology Center in Karlstad, Sweden
- Full-scale tissue pilot machine since 1985
- Pilot plant personnel
- R&D project managers
- machine, chemical system and pulping operators
- laboratory personnel
- More than 1,000 customer trials
- Possible machine configurations
- Advantage DCT Process (conventional)
- Advantage NTT process (hybrid)
- Advantage QRT process (hybrid)
- Advantage ThruAir process (TAD)
- Other confidential configurations
- Full-sized flexible pilot machine
- 3-layer headbox with dilution control simulation of 1, 2 and 3 layer set up
- 2 x 16 feet TAD cylinders & 15 feet Yankee
- belted reel
- calender, heated steel/steel or rubber/steel
- variable creping doctor
- numerous chemistry possibilities
- 3 pulp chests with flexible approach system
- Fully equipped laboratory
- paper tests
- pulp tests
- Valmet Automation system including DNA
- General information
- Machine speed: Max 2000 m/min (6500 fpm)
- Sheet width on reel: 500 mm (20 in)
- Basis weight range: 11-50 gsm (7-30 lbs/R)
Tissue Converting pilot centers
Lucca, Italy
- Pivot Lab
- Sincro Pilot Line (300mm)
- Full speed Constellation S6 Pilot line (700 mm)
Green Bay, USA
- Pivot Lab
- Full speed Sincro Pilot Line (600 mm)
Sao Paulo, Brazil
- Pilot Line Mandrel Technology (500 mm: 200 m/min)
- Pilot Line Napkin Technology (heads 24, 30 and 33 cm)
Joinville, Brazil
- Pivot Lab
Tissue news
Explore our customer success stories and learn more about our full-scope offering in the tissue industry.